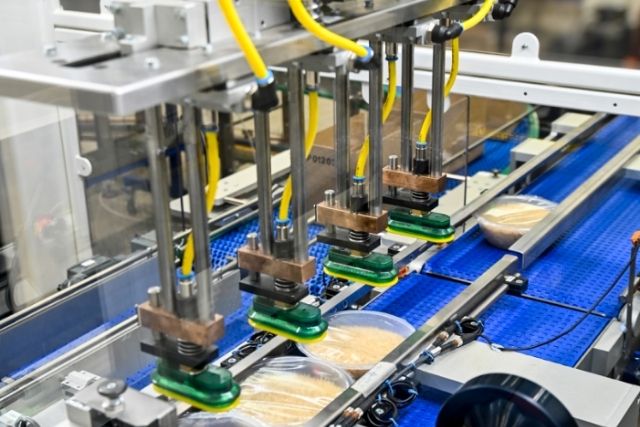
Factory automation has become a particularly hot topic in recent months. The dual impacts of Covid-19 and Brexit have led to a shortage of workers across many UK manual jobs. As a result, UK companies are increasingly looking into the prospect of using automation to reduce downtime and increase work efficiency, as has been done successfully elsewhere in the world.
In general, automated food processes ensure food products are picked and packaged uniformly, with fewer mistakes and variances between individual products. Machines are not prone to human error, sickness or tiredness, and so also offer more predictable, and overall more consistent returns for a company’s investment. Employing such technology is therefore one of the main ways to reduce downtime in your production line.
What is end of line automation specifically?
End of line automation in the food industry refers to the automated processes that happen towards the end of the food production line. It covers the picking, packing, verification and quality checking, and delivery preparation of foods delivered to retailers and wholesalers.
Benefits of end of line automation
- Meet increased demand from an ever-growing growing population
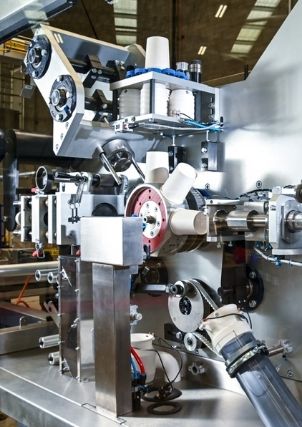
- Better allocate labour to ensure workers are used in the most suitable place along your food production line. (It is an oft-cited misnomer that automation might replace factory workers, when instead it can lead to them being better deployed and can even help create job opportunities).
- Improve worker health by limiting the number of repetitive strain injuries they are likely to develop over time due to being moved away from the end of line process
- Speed up productivity by eliminating downtime and human error while increasing production efficiency at the end of the line.
However, because of the specificity that can often be needed in food packaging, end of line automation can be tricky to get right. Even a slight miscalculation can cause food to be placed untidily and inefficiently. In addition, automation needs to replace the manual quality and verification checks that operators do with the human eye and feel. This is a core reason food businesses still rely on human packers at the end of their food production line. If you are going to switch to automation, the subtleties involved make choosing the right partner absolutely essential.
Picking the right automation partner
The client I recently started working with is a true expert and market leader in the field of end-of-line food factory automation.
Staffed with well over 100 automaton engineers, they’ve installed more than 6,000 industrial automation systems and exported more than 85% of their work worldwide.
Where the food industry is concerned, they work on automation projects of all kinds, including:
- Refurbishing existing technology to ensure optimum running of the entire production process – including the tricky end of line part
- Standardising technology across factory areas so that old systems can be upgraded to work together with newer ones, allowing a food production business to reduce downtime and increase efficiency across the board
- Implementing original bespoke automation solutions that solve the often-unique problems of each food production business through innovative thinking and cutting-edge robotics
- And even fixing other company’s mistakes by working with food businesses to identify the problems in their current setup and offer upgrades or alternative solutions.
Considering automating your food production line?
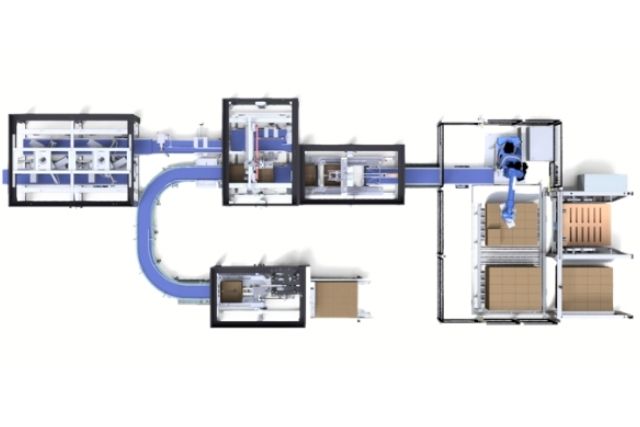
The importance of end of line automation in the food industry is only going to grow as the population booms and the evolving impacts of Covid-19 become clear. With higher efficiency, less downtime and zero requirements for social distancing measures, automation looks set to be relied on by more and more food production businesses. If you’re not at least considering it, it’s my belief that you’re essentially setting your business up to be left behind down the line.
If you are considering it, however, then I can help. Get in touch to discuss how automation could help with reducing downtime and increasing efficiency in your food production business.