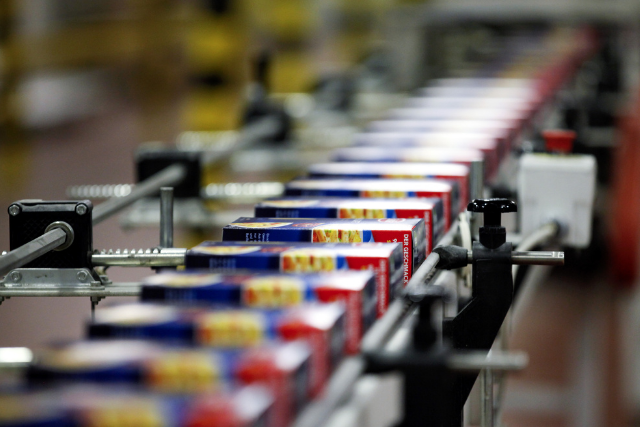
Much has been written online about the importance of food production automation at both the processing and the packing end of the factory line. (In fact, I recently explored end of line automation myself). However, secondary food packaging processes often get overlooked. As a result, it’s one big area of automated food production where businesses can often make significant efficiency gains with the right connections and investments.
What is secondary packaging in food production?
Secondary packaging is essentially the outer shell, carton or box that carries the product’s branding, barcode and legally-mandated information.
While primary automated food packaging systems revolve around measuring, dosing and filling the packaging that comes into direct contact with food, secondary packaging processes are concerned with covering those first containers with boxes, cases, or sleeves – all predominantly made of cardboard – or in many instances supermarket trays.
Why moving to automating secondary packaging asap just makes sense
There are a number of issues that make automation not just an attractive idea, but something nearer a necessity for food businesses in the current climate. At the same time, there are also a number of logistical challenges that companies considering these measures must seek to overcome.
Here are some of the salient points:
Labour Shortages
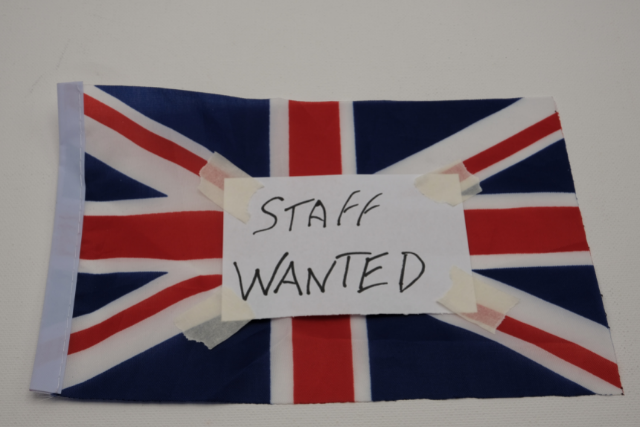
Secondary food packaging is often done by hand, however the combination of Brexit and Covid has led to a huge shortage of manpower. Much of the industry is struggling with as much as15-20% shortage of staff. Brexit has resulted in a shortfall of workers from eastern and southern Europe who often took those roles. Covid meanwhile has caused decreases in efficiency, with staff sickness rates spiking and access to factory sites not always possible for people in large numbers.
Additionally, there are regional concerns to consider. Some products are in greater demand in specific seasons, meaning factories need to increase headcount for only a few months a year. However, what happens if the surrounding region simply doesn’t have enough cost-effective housing to support the short-term influx of workers? The ongoing housing crisis means this is a problem that’s not likely to go away any time soon, which for those businesses affected will make the drive for automation in secondary food packaging processes all the more important.
Factory floor space
Many robotic food packaging providers offer a standard off the shelf solution for a business’s packaging needs. However, food factories certainly don’t come in uniform sizes, and most have a very limited floor space, where the packaging process is designed to be as efficient as possible. Bespoke automated food packaging systems designed to fit a factory’s footprint can allow food manufacturers to actually increase efficiencies, without needing to make significant and expensive changes to their factory’s floorplan or even having to move to new premises.
The global semiconductor chip shortage
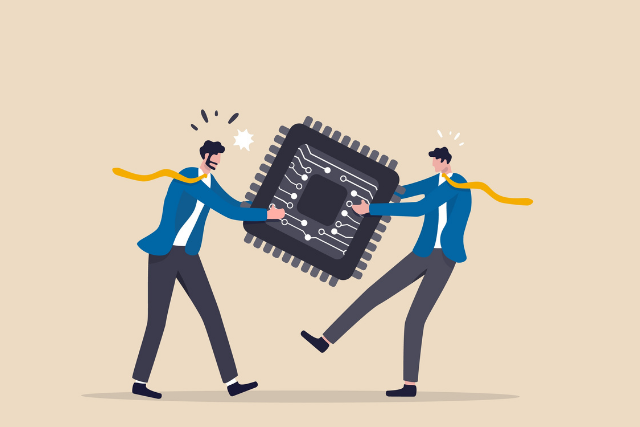
One area of food production that food manufacturers do need to constantly keep on top of is food authenticity.
The ongoing shortage of semiconductors caused by the Covid-19 pandemic has had a significant impact on the consumer world. Everything from automobile production to videogames console availability has been drastically curtailed, and automation in food packaging has certainly not escaped similar shortages and delays.
So, in that sense it’s, a little bit of a catch 22. While automation might seem the solution to the labour issue that Covid has in-part caused, Covid is also a bit of a blocker to businesses adapting the technology immediately.
That being said, the efficiency benefits of food production automation will be felt for a long time after the current shortages end. And with lead times of many months in some places, the sooner businesses make the call to switch, the sooner they can feel those benefits.
Want to automate your secondary packaging processes sooner?
If you want to establish automation in food manufacturing in the middle, or at the end of your packaging process, you could contact companies with off-the-shelf solutions. However, they’re likely to be reliant on standard semiconductor supplies from parts of Asia.
Thankfully, there is an alternative.
I’m currently working with a client who is able to design and build their own CNC automation equipment, lines and delta robots, often with a far faster turnaround.
With the food industry currently lagging behind peers like automotive and aerospace in terms of automation, and economic uncertainty a continuing trend even after the worst of the pandemic, now is an ideal time to look at future proofing your mid and end-of-line food packaging processes.
If you’d like to know how my client can help you, get in touch with me today.
Or for more musings on the food industry and how innovative technology and thinking can help your business adapt to trying times, check out the blogs below.